Si vous habitez ou circulez dans la région de Charleroi, vous connaissez certainement Thy-Marcinelle. Implantée en bord de Sambre depuis 1970, c’est grâce à sa capacité d’adaptation et à son regard tourné vers l’avenir que l’histoire de Thy-Marcinelle se poursuit jusqu’à ce jour. Parmi les différentes évolutions qui lui ont permis de continuer à prospérer, se trouve une méthode de production particulière de l’acier : celle de la coulée continue. Cette méthode a été utilisée pour la première fois en Europe, en 1964, dans une usine du groupe Riva. Elle a été importée sur le site de Thy-Marcinelle en 1992, avec la construction de la nouvelle aciérie électrique.
Les différentes méthodes de coulée de l’acier
L’acier en fusion (env. 1600°C) peut être coulé de différentes façons :
– Par injection sous pression dans un moule mécanique à l’aide d’un piston, ce type de moulage permet de fabriquer en petite série des pièces légères.
– Par coulage au moyen d’une louche ou d’une poche en fonderie, lorsqu’il faut produire une quantité limitée de pièces, voire un prototype.
– La coulée en lingot : le lingot est un moule de grande dimension dont l’intérieur est recouvert de réfractaire. Une fois démoulé, le lingot d’acier est prêt à être laminé.
– La coulée continue est désormais la méthode la plus utilisée par l’industrie sidérurgique.
En quoi consiste une coulée continue ?
L’acier en fusion est versé dans la lingotière (moule) vibrante placée en position verticale. L’acier se refroidit et se solidifie au contact des parois de la lingotière qui est refroidie énergétiquement. À mesure que l’acier liquide est versé dans la lingotière, l’acier solidifié est récupéré à l’autre extrémité – en continu – et coupé à la longueur voulue. On obtient ainsi des brames, des blooms ou des billettes qui sont les demi-produits de la sidérurgie.
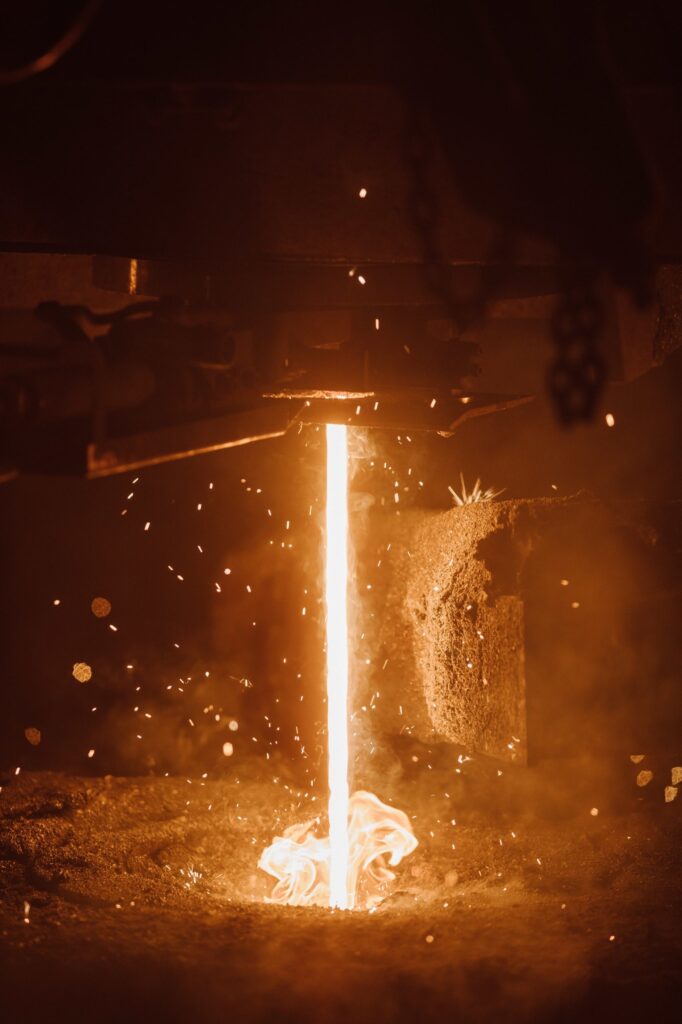
Les avantages de la coulée continue
La coulée continue permet de produire automatiquement d’importantes quantités de produits semi-finis de plus grande longueur et de qualité supérieure par rapport aux lingots.
Ainsi, en limitant les chutes de fabrication, on estime que la coulée continue a permis à la sidérurgie de gagner en productivité et de diminuer sa consommation énergétique de 30%.
Cette méthode efficiente, permet aussi de diminuer le besoin en énergie grâce à l’enfournement à chaud des billettes de la coulée continue dans le four de réchauffage avant laminage.